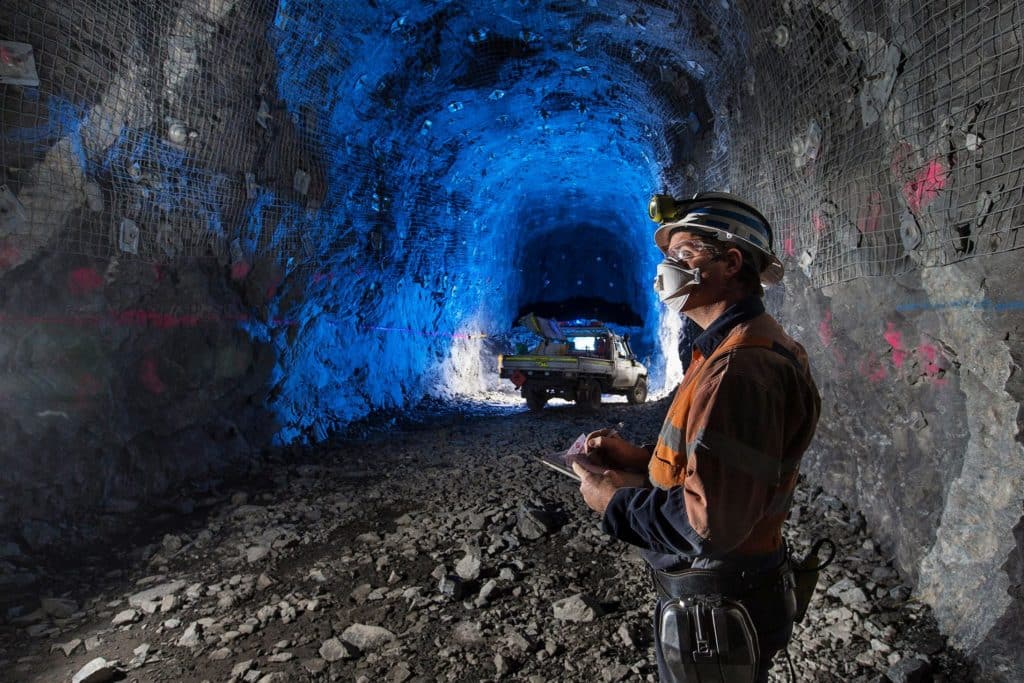
From the world’s largest underground copper operations in Chile and Australia to leading gold mines in Canada, United States and Mexico, every mine is unique. The majority of the world’s mines are located in some of the harshest environments and are used to extract ore from below the surface.
Every mine is unique due to the ground conditions, design, mining method, composition of surrounding rock, the shape, orientation of the ore deposit, ventilation, the amount of development work done or that may be necessary and whether the values are regularly or irregularly distributed.
Coal extraction makes up the largest portion of underground mining and represents 60% of worldwide coal production. Other than coal, underground methods are also frequently used to mine gold, copper, diamonds and other metals.
Currently, the deepest underground mine in the world is the Mponeng gold mine situated in South Africa. In 2019, the Mponeng produced 244,000 ounces of gold! As of 2020, the operating depth ranged from 3.16km to 3.84km below the surface. Future mining is expected to further deepen the shaft bottom to 4.22km and it is expected to be in operation until at least 2027.
The history of underground mining
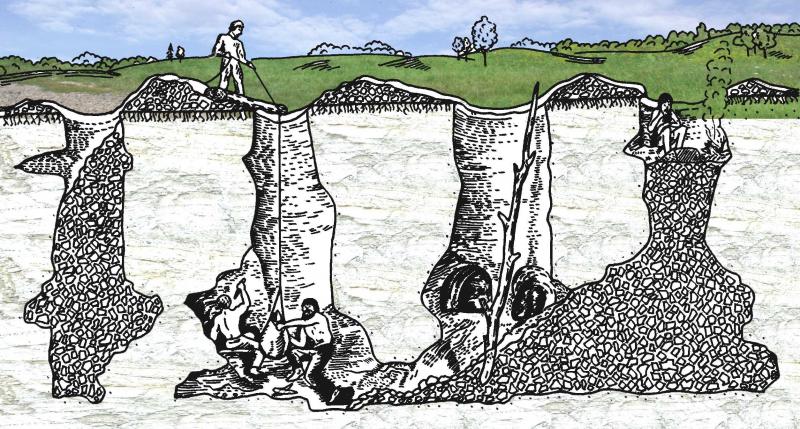
Archaeological discoveries indicate that mining was first conducted in the New Stone Age (around 8000-2000 BCE) where shafts of up to 330ft were sunk in soft chalk deposits in France and Britain by means to extract flint pebbles and minerals. The flint pebbles were used to make scrapers, knives and arrowheads as it could be broken down into sharp-edged pieces. The minerals extracted from the mines were often used as pigments.
The oldest known underground mine dates back more than 40,000 years ago and is located in Bomvu Ridge, Eswatini. It is believed that this mine was used in burial ceremonies.
What is underground mining and why do we use it?
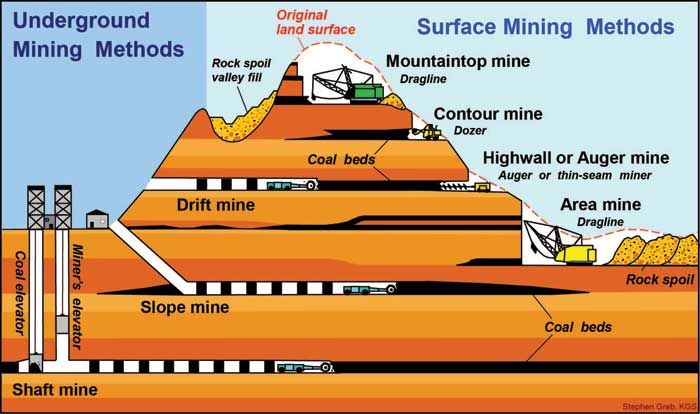
Underground mines are an alternative to surface mines, however both methods do have their positives and negatives and are used in different ways. One of the major drawbacks of surface mining is the method destroys large areas of land, demolishing landscape and natural habitat to recover ore. Whilst underground mining requires an array of resources, equipment and finance, the method is often favoured to surface mining as it has less environmental impact.
The method of mining used depends greatly on the mineral’s location. Surface mining tends to be used when the deposits to be extracted are not very far below the surface and are quite easily accessible. With underground mining, the deposits are much deeper into the surface and require tunnels to go further into the seam.
The underground mining process
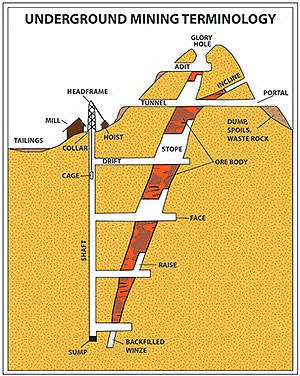
There are several methods of underground mining and the type used will be dependent on the individual mines conditions and variables. Generally, there are hard-rock and soft-rock underground mines. Coal deposits are usually found in relatively soft rock. Gold, diamonds and copper on the other hand live in metamorphic rock which is relatively hard. There are two main methods of underground mining which are room and pillar and longwall.
The oldest mining method, room and pillar, is when deposits are mined by cutting a network of ‘rooms’ into the seam and leaving behind ‘pillars’ to help support the roof of the mine from collapsing. After mining out the ore within the area the pillars are then removed for a safe collapse and fill to take place. However, this method is not the most efficient. This process is primarily used for flat-lying or dipping ore bodies.
The second technique, longwall, utilizes a shearer which is a large machine with a rotating drum that alternates back and forth across the ore seam. The equipment pushes forward during production enabling it to avoid overlying rock, making high levels of production and greater safety.
With this method, large deposits are identified beneath the surface which are then extracted in slices by undercutting, which is then blasted and drilled. The fragments are placed on conveyor belts until the entire ore block is extracted. With the longwall technique, the roof of the mine is supported by longwall shields which provide cover for the conveyor belt, workers and any machinery. This method can produce around 20,000 tonnes per day!
The main method of access to an underground ore body is a vertical opening called a shaft. The shaft is excavated from the surface downward to a depth somewhat below the deepest planned mining limit. At frequent intervals along the shaft, horizontal openings called drifts are driven towards the ore body. Each of these major working horizons is called a level. The shaft is equipped with elevators (cages) by which the mine workers, machines and material use to access the mine. The extracted ore is transported up to the surface in special carriages named skips.
Omnia Machinery are a reputable mining equipment trader and we stock a selection of quality used mining machinery suitable for numerous projects such as: Underground Trucks, Underground Excavators, Underground Loaders, Underground Rock Drills and Underground Dumpers. All of our machines that we stock come from reputable manufacturers such as Atlas Copco, Sandvik and Tamrock – giving you confidence that you will find a machine suitable for your project specifications. If you would like any further information on our Underground Mining machines, be sure to contact us!