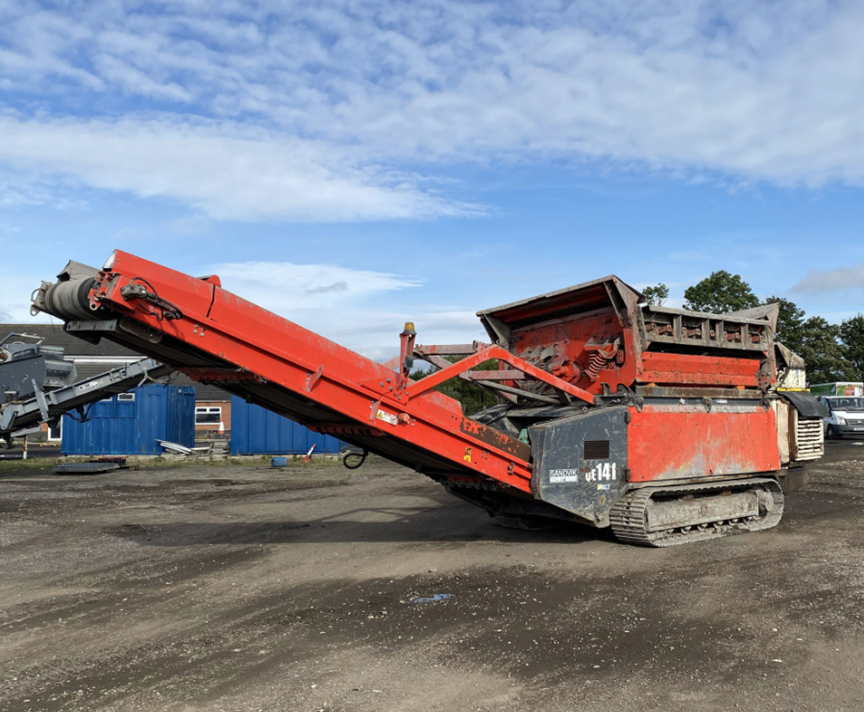
A screen is a machine used to separate mixed materials into different grades which usually falls into two categories, dry screening and wet screening. The machinery can also be categorised into moving screen and static screen machines, and if the screens are horizontal or inclined. Screens can be found on most construction sites and quarrying operations. Once the crusher has finished the materials are then fed into the screener ready for organizing. Screening equipment can stand alone, however, when you pair screening equipment with a crusher, you create a full-circuit system. These systems work together to create a flawless material handling process. Although screens can be used without crushers, a full circuit system is the most effective way to mine and separate materials to create something sellable.
When working in construction you need to ensure you have the correct tool for the job if you want to get maximum efficiency. When it comes to crushing if you require a specific particle size, then there are several parts of screening equipment that must vary to get the result you need. These variables can be the screen material, size, slope, hole openings, number of decks and type of vibration motion. Because of their unique features vibrating screens offer specific benefits over other material processing equipment.
History
Screening, which was also known as sieving, winnowing has been around for a long time. It was used in ancient times for the cleaning of cereals as they separated their grains from sand and straw, a process mainly used for barley and wheat crops. In 1737 the winnowing machine for corn named the Fanner was created. With the first industrial revolution, the winnowing process was mechanized, and the fanning mills were invented. These machines would clean the grain and separate it from dust and seeds. After the first crusher was patented in 1858, great efforts were made to improve screening technology.
Types
Inclined Screens
Regarded as the most popular type of screen, the inclined screener has a number of options including two and four bearing, high-speed, and high-frequency screens. When it comes to finer particles it is a job for a high-frequency screener. This machine uses intense vibrations to separate minerals. An electromagnetic vibrator connected to the surface of the screen controls the strength of the vibrations as materials are added from a conveyor. This screen can often be used as a secondary screening measure to further remove the finer particles either before or after the primary screening process.
Horizontal Screens
The modern-day horizontal screen is fitted with two vibrating motors which rotate in the opposite direction to each other. This rotating motion causes the frame of the screen to vibrate in a linear or straight-line motion perpendicular to the plane of the motors. Usually, the motors are positioned at an angle of 50 degrees to the screen’s surface. The horizontal vibrating screens frame can be positioned from 10 degrees uphill to 15 degrees downhill, depending on the application. But the maximum capacity is achieved in the uphill position, causing the formation of a pool at the feed end of the machine.
Vibratory Screeners
The most popular screener found on a construction or quarry site for bulk applications is the vibratory screener. As the materials move across the screen it creates vibrations in order to shake out the smaller particles and remove any clumps. This is usually the easiest and most effective way to separate materials by size. A vibratory screener can come in a range of different sizes and can process large volumes of material in certain applications.
Trommel Screens
Trommel screen also known as a rotary screen is perfect for separating materials with great precision. The trommel includes a cylinder which is usually divided into several sections depending upon the requirements of the situation. The mesh holes in the cylinder are arranged from small to large. A trommel screen is made up of a motor, reducer, roller device, frame, sealing cover, inlet and outlet. The cylinder spins to sort through the material as it is fed into the machine. Air is added to make the materials lighter and drier. The tumbling action also allows maximum contact time with the screen so that the fine materials can get through quickly. Even though it is designed with wet material specifically in mind it can sort through dry substances quickly as well.
Here at Omnia Machinery, we offer a wide range of quality used quarry equipment such as Jaw Crushers, Cone Crushers, Impact Crushers, Screeners and Shredders. We offer machinery from the leading manufacturers such as Sandvik, Kleemann and McCloskey. As with all of our heavy equipment, each machine is thoroughly inspected, tested and serviced before shipment, ensuring you’re supplied with only the best for your project. Browse our quarry machinery here.