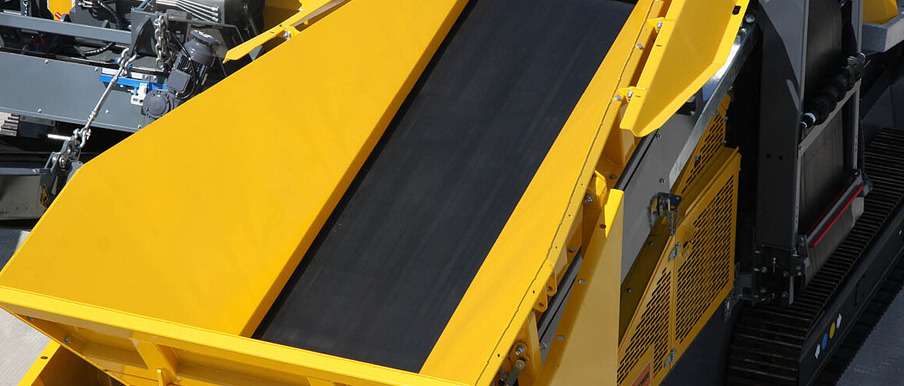
Apron Feeders and Belt Feeders, which is the better option? This is a commonly asked question, but as is with most equipment the answer is “it depends”, both have their strengths and weaknesses depending on the application. In this blog we will discuss what belt and apron feeders are how and where they are used, and which may be more suited to your job.
What are they?
Feeders are typically located at the base of the hopper in most crushers and screens, their task is to move the material at a steady speed from the hopper onto the screen, crusher or feed conveyor.
The apron feeder is built from undercarriage chains, rollers and tailwheels, similar to the type of tracks you would find on a bulldozer. Two of these undercarriage systems are placed side by side and are joined by heavy-duty grouser bars. The links are sealed to stop materials from penetrating and wearing out the system. Due to the structure, apron feeders are more suited to the heavy-duty projects and can handle rocks up to 600mm+.
Belt feeders are feeders that operate with a single endless hardened rubber belt, a drive drum, an idle drum, and more rollers. This system allows transportation of material often smaller than 300mm over longer distances and at higher speeds. However, belt feeders wear a lot quicker and won’t take substantial hits that apron feeders can and are suited to applications that could have a lot more liquid runoff.
Specific Advantages/Disadvantages
Apron Feeders
Pros
- Built from hardened steel
- Not prone to slips
- Can take heavy loads (rocks up to 600mm)
- Can take impacts
- Handles many different types of materials
- Better for bark and mulch applications
- Wear takes a lot longer
Cons
- Larger upfront investment
- Slower moving
- May be worn out by very wet fine material
- May have some leakage of fines
Belt Feeders
Pros
- Perfect for small material wet or dry
- Better suited to smaller materials (max size 300 mm)
- Moves faster
- Less upfront cost
Cons
- Often require more maintenance
- Cannot tear with sharp material
- Dropping material on to belt may cause damage
- Possibility for material to slip on the belt
It’s important to note that different feeders serve different purposes, and some companies may use both types across various machines. For example, Keestrack use apron feeders in all their heavy-duty scalping screens, which are typically used in primary applications, while they utilize belt feeders in the H4e, a machine commonly employed as a secondary or tertiary crusher.
Application
Apron feeders are best suited for primary applications, especially when handling large, heavy materials with sharp edges that may be dropped from a height. They are also ideal for challenging materials like bark, mulch, or recyclables that tend to slip on belts. While apron feeders are more durable and require significantly less maintenance, they come with a higher upfront cost.
On the other hand, belt feeders excel in secondary applications, where smaller aggregates that aren’t dropped from height are handled. They are more suited to transporting materials over longer distances. However, they require more frequent servicing and are more prone to damage, which can add to their long-term costs.
In conclusion, the choice between the two options depends on the specific application and the unique needs of your quarry. When comparing machinery, it is key to recognize that components like feeders can significantly impact ROI. Therefore, selecting the correct feeder for the intended application is essential for optimizing performance and profitability.
Here at Omnia Machinery, we offer a wide range of quality used quarry equipment such as Jaw Crushers, Cone Crushers, Impact Crushers, Conveyors, Screeners and Shredders. We offer machinery from leading manufacturers such as Sandvik, Kleemann and McCloskey. As with all of our heavy equipment, each machine is thoroughly inspected, tested and serviced before shipment, ensuring you’re supplied with only the best for your project. Browse our quarry machinery here.